Chargeurs
Wilo Salmson repense sa logistique en profondeur
Dans le cadre d'un projet de refonte sur quatre ans, l'entreprise Wilo Salmson France a travaillé sur de nouveaux concepts logistiques pour son site de Laval (53).
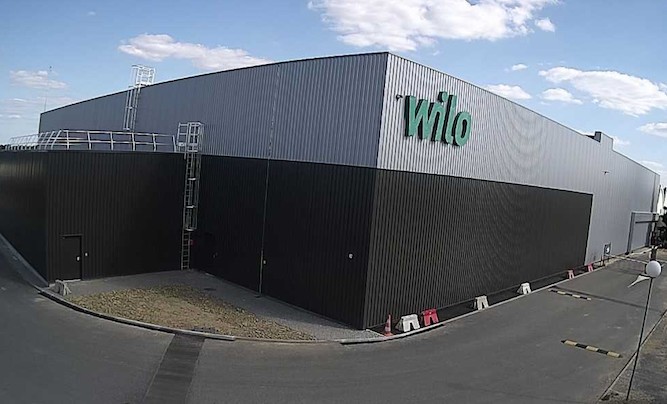
©
Wilo Salmson France
Regroupant les deux structures françaises du Groupe Wilo SE (Pompes Salmson et Wilo France), Wilo Salmson France se spécialise dans la conception et la fabrication de pompes et systèmes de pompages pour l'industrie et le bâtiment. Basée dans les Yvelines, cette emploie regroupe aujourd'hui près de 760 salariés sur trois sites en France avec un chiffre d’affaires de 242 millions d’euros en 2017. Dans le cadre de son projet « Laval 2020 » démarré en 2016, Wilo Salmson France a souhaité repenser les process de son usine de production et de sa plateforme logistique, basées en Mayenne, avec un focus particulier sur l'optimisation logistique. Objectif : gagner en productivité et préparer les évolutions futures.
Côté logistique, ce travail en interne est passé par la mise en lumière des lacunes de l'organisation des flux, avec un tiers des trajets en chariot automoteur se faisant à vide et un manque de flexibilité global. Pour cela, Wilo Salmson France a d'abord crée une zone de picking sur le site logistique de Louverné (53). Sur ce site de 12 000 m² réalisant quelques 750 expéditions chaque jour, l'entreprise a fait construire une extension de 1 300 m² en avril 2018, où les collaborateurs peuvent prélever des composants dans la zone de stockage de masse puis conditionner des lots de composants destinés à alimenter l'usine située à 4 km de là. De quoi réduire les stocks de composants sur le site industriel.
Kitting et train takté
Une zone de kitting de 2 000 m² sur le site de production de Laval (53) a également été mise en place, en lien direct avec la zone de picking de Louverné. Dans cet espace, des kits de composants sont préparés pour alimenter les lignes de production du site. Un pilote pour l'approvisionnement des îlots de fabrication par un système de train takté (les pièces avancent face aux collaborateurs qui ne bougent pas de leurs postes) est également à l'essai pour, à terme, desservir l'ensemble des unités autonomes de production de l'usine. Les avantages : plus de sécurité pour le personnel avec une réduction du nombre de chariots automoteurs en circulation, un moyen de transport identique pour les composants ou encore une réduction de la taille des lots.
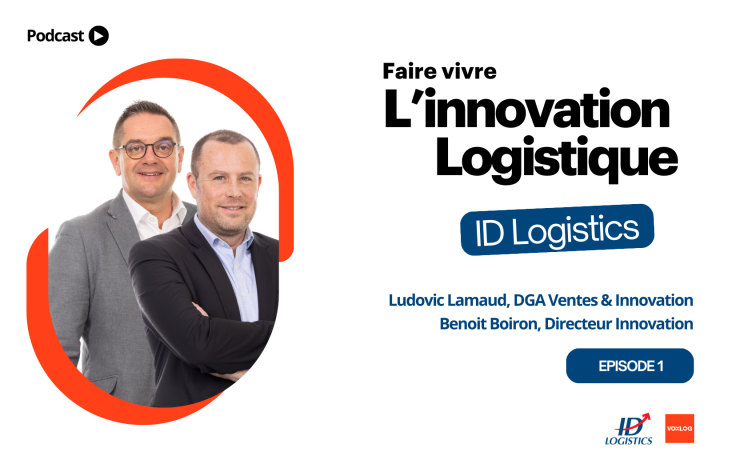