Innovation
Avec Stöcklin, Omega rend son entrepôt plus intelligent
Avec ses solutions innovantes, Stöcklin Logistik permet aux entreprises de se lancer dans le concept de l'usine intelligente, aux processus d'approvisionnement minutieusement cadencés. C'est le cas de l'horloger Omega (groupe Swatch), qui a totalement repensé l'organisation de son site en Suisse.
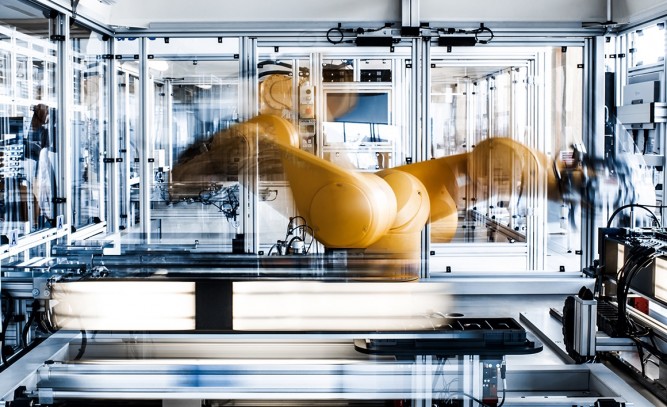
©
Omega
La mise en réseau, la transparence de l'information, l'assistance technique et les décisions décentralisées forment les pierres angulaires de la « Smart Factory » (usine intelligente). Les entreprises qui allient systématiquement production et logistique et les automatisent au plus haut niveau, créent une base solide sur laquelle le principe de « l'usine intelligente » peut croître et se développer. Dans cette nouvelle configuration de la Smart Factory, l'homme continue à jouer un rôle essentiel. Les technologies de pointe rompent la monotonie des tâches et créent une ambiance propice à accroître la motivation et la satisfaction des employés.
Des processus d'approvisionnement minutieusement cadencés
Comme toujours, lors du développement de nouveaux sites de fabrication, la production reste au centre de l'attention. Alors qu'une importance secondaire est accordée à la gestion des flux de matériaux. Mais à une époque où l'industrie 4.0 basée sur l'idée centrale d'une usine intelligente en partie déjà réalisable aujourd'hui, une telle différenciation, à savoir une planification n'intégrant pas la gestion des flux de matériaux, est de plus en plus remise en question. Il est nécessaire de concevoir des concepts holistiques pour que l'ensemble des processus de production et de logistique puissent être intégrés au sein d'un même réseau et synchronisés de manière flexible. Un autre avantage est la réduction de l'encombrement grâce à la réduction des stocks.
En plus des centres de distribution automatisés, le groupe suisse Stöcklin a récemment mis en œuvre un certain nombre de projets clés en main dans ce segment de la logistique de production en particulier, en intégrant les objectifs stratégiques et commerciaux de ses clients. L'optimisation individuelle de l'espace, du temps et des ressources est prise en charge par une large gamme de logiciels et matériels issus de notre propre production, qui sont entièrement fournis et mis en œuvre par le prestataire international et entrepreneur général spécialisé en intralogistique dont le siège se trouve à Dornach, Suisse.
Un travail de qualité suisse sans compromis
Omega, une marque du groupe Swatch, a également fait confiance au prestataire de systèmes intralogistiques pour la construction d'une nouvelle usine de montres de luxe à Bienne (canton de Berne). Le nouveau site de production, construit selon les critères écologiques ultramodernes et s'intégrant harmonieusement dans le paysage urbain, réunit sous un même toit l'assemblage et le contrôle qualité ainsi qu'un entrepôt de petites pièces entièrement automatisé avec technologie de convoyage intégrée. Il existe également des zones de conditionnement et de mise à disposition de produits finis, prêts à être expédiés. « Le déploiement d'un nouveau concept logistique devrait permettre d'optimiser les flux de matériaux et les installations de stockage et d'adapter la préparation des commandes et les capacités de stockage aux besoins futurs », explique Domenico Palombo, responsable des marchés francophones au sein de la division Équipement de Stöcklin Logistik AG. La priorité était de relever le niveau de performance et de disponibilité tout au long du cycle de vie de l'installation et de garantir une flexibilité maximale. Il s'agissait également de réduire les coûts associés aux processus.
Depuis sa mise en service fin 2017, l'entrepôt de petites pièces (AKL) entièrement automatisé est au cœur du nouveau bâtiment de production réparti sur cinq étages, construit pour ainsi dire autour du système intralogistique. L'entrepôt gère une grande variété de composants et de têtes de montres qui sont stockés ou déstockés selon les étapes de travail et prélevés sur les différents étages pour la préparation de commandes. Des spécialistes des domaines respectifs assemblent avec une extrême précision en salle blanche le mécanisme d'horlogerie avec cadrans, aiguilles, boîtiers et bracelets. Les contrôles et les tâches logistiques sont exécutés en partie par des robots. Pour terminer, les montres assemblées sont emballées et envoyées au service expédition via une technique de convoyage spécialement conçue à cet effet.
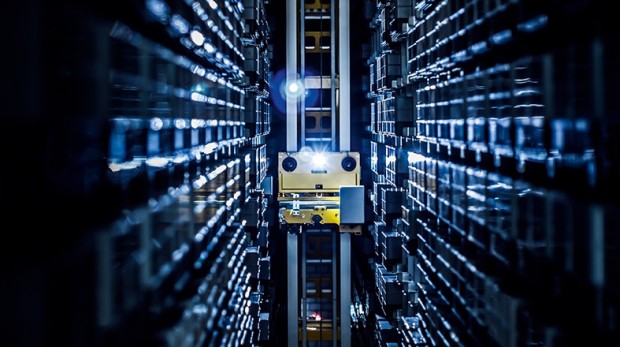
©
OmegaEntrepôt automatique pour petit matériel comme aide à l'assemblage
L'entrepôt pour petit matériel peut accueillir plus de 30 000 conteneurs à double profondeur. Afin de protéger au mieux les marchandises de valeur dans l'entrepôt, toute l'installation a été traitée par inertage. Pour le client Omega, le système de prévention du risque incendie prévoyait une réduction de la teneur en oxygène de seulement 15,2 %. De cette façon, les mesures préventives sont suffisantes pour s'assurer qu'aucun incendie ne puisse se déclarer. L'entrepôt est équipé de quatre transtockeurs de la famille BOXer de Stöcklin Logistik, chacun intégrant un dispositif de manutention de charge automatique. À ce sujet Domenico Palombo déclare: « L'efficacité énergétique est un sujet central depuis le début. Nous satisfaisons à cette exigence avec la construction légère des appareils BOXer, qui, grâce à ce principe de conception et à performance égale, sont les plus faibles consommateurs d'énergie parmi les transstockeurs de petit matériel disponibles sur le marché. »
Avec sa conception modulaire, le BOXer est également conçu pour offrir un maximum de flexibilité et de modularité. Grâce au WMS (système de gestion des stocks) avec contrôle intégré des flux de matériel, des stratégies de stockage et de déstockage sont mises en œuvre en permanence, en intégrant les besoins quotidiens. De ce fait, les transtockeurs de petites pièces ne fonctionnent pas toujours à la vitesse la plus élevée mais adaptent leur vitesse en fonction des exigences. L'usure des composants et les besoins en énergie sont ainsi réduits, ce qui permet d'économiser les ressources et d'éviter des coûts d'exploitation inutilement élevés. Parallèlement, des ressources suffisantes sont libérées pour fournir les performances maximales requises en période de pointe au niveau du système.
L'installation (27 x 10 x 14 m – L x l x h) s'étend sur trois étages - du sous-sol au premier étage. Les étages restants sont reliés au système par des ascenseurs qui déplacent les marchandises sur un axe vertical. Pour le stockage et le transport, Omega utilise des conteneurs spéciaux de 305 x 405 x 230 mm qui peuvent être identifiés au moyen de codes-barres EAN pour articles individuels, dont deux sont apposés sur chaque conteneur. Au total, environ 1 000 transferts de conteneurs par heure sont possibles au sein de l'entrepôt automatisé. Le système de gestion des stocks intégré agit comme un organe de contrôle central, garantissant la transparence des stocks de bout en bout et l'utilisation efficace de toutes les ressources.
Mécanismes de protection intégrés pour l'opérateur et les marchandises stockées
Une autre particularité : ces conteneurs sont dotés de couvercles anti-poussière spéciaux avant l'entreposage, afin de préserver les têtes de montres et les composants de haute qualité. Lors de la sortie d'entrepôt, les couvercles anti-poussière sont à nouveau enlevés. Comme les tâches sur la durée peuvent devenir monotones pour les opérateurs, Omega utilise des robots pour les exécuter. Le WMS vérifie également quand un conteneur ou un couvercle a été nettoyé pour la dernière fois. Lorsque le cycle de référence est atteint, le système déclenche automatiquement un acheminement vers la machine de nettoyage au niveau inférieur. « Compte tenu de la valeur des marchandises stockées, il est impératif de créer un environnement aussi stérile que possible, que ce soit pendant le stockage et le transport, pour éviter l'infiltration des plus infimes impuretés », explique Domenico Palombo. Une autre exigence concernait la question tout aussi importante de la protection contre le bruit. « Les tâches réalisées dans les ateliers requièrent une concentration maximale, c'est pourquoi il est essentiel de réduire le bruit et les nuisances sonores à un niveau minimum », poursuit l'expert en intralogistique. Le niveau des émissions sonores a été réduit en conséquence afin que les ouvriers puissent continuer les tâches exigeantes sans être incommodés.
De plus, des gaines installées à chaque étage du bâtiment de production empêchent les particules de saleté d'entrer à l'intérieur des locaux. Aujourd'hui chez Omega, la production est également totalement dématérialisée. Toutes les informations nécessaires au montage peuvent être consultées sur écran ou tablette. Dans l'entrepôt de petites pièces BOXer entièrement automatisé, le système de gestion des stocks satisfait également à cette « exigence de pureté » en mettant en œuvre un système de gestion des stocks et de contrôle des flux de matériaux entièrement numérisé. Alors que l'entrepôt de petites pièces 100 % automatisé sert à entreposer les têtes et les composants de montres ainsi qu'à préparer les pièces pour l'assemblage, les montres finies sont stockées dans des entrepôts spécialement conçus. L'approvisionnement et l'enlèvement s'effectuent à l'aide d'une nouvelle technique de convoyage de conteneurs adaptée par des experts suisses en intralogistique aux exigences particulières des moyens de dispositifs d'aide au chargement utilisés ici. Le système WMS contrôle également l'ensemble du flux de matériel conformément aux ordres de commande, jusqu'à l'emballage et à l'expédition par le transporteur, et gère le stock des magasins de produits finis.
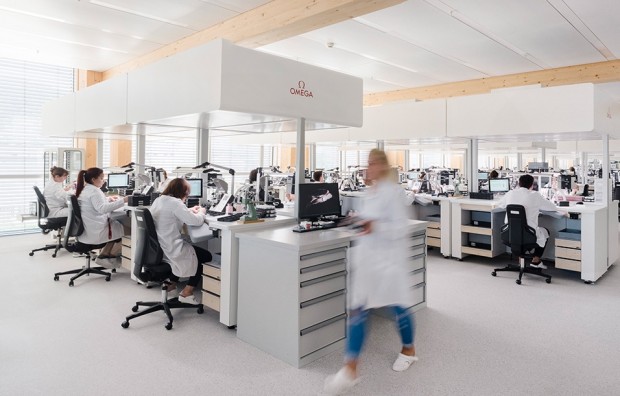
©
OmegaPoursuivre la réflexion sur la place de l'innovation et de l'excellence
L'intégration directe d'un magasin de petites pièces 100 % automatisé avec technique de convoyage horizontal et vertical à l'intérieur de la zone d'assemblage garantit la disponibilité totale et immédiate des pièces nécessaires pour une livraison en « juste à temps ». Cela répond également aux critères définis par le concept de Lean Production, qui met l'accent sur l'utilisation la plus économe possible de toutes les ressources de production en un minimum de temps. Dans le même temps, Omega a su répondre à ces exigences en relevant le niveau de ses performances d'exécution. L'installation intralogistique automatisée contribue de manière décisive à garantir la rapidité et le respect des délais de livraison attendus par le client final et à offrir une expérience d'achat optimale en ligne ou en magasin.
La fiabilité au niveau technologique, la transparence dans le suivi des commandes avec une traçabilité à 100 % des composants, des temps de passage courts et des cycles d'approvisionnement spécifiquement adaptés, associés à des coûts de processus modérés, sans oublier une flexibilité maximale, sont ici autant de facteurs décisifs. Le système de production entièrement connecté avec logistique intégrée mis en œuvre pour le fabricant suisse de montres de luxe sur le site de Bienne convainc également par des stratégies zéro défaut et un environnement de travail silencieux pour le bien-être du personnel. Autant de conditions qui, au-delà de l'automatisation, contribuent à l'amélioration de la productivité globale. Les exigences en matière de disponibilité de l'installation restent par conséquent élevées. La qualité de service était donc également un critère déterminant pour Omega. En cas d'urgence, l'équipe de Stöcklin Logistik est disponible 24 heures sur 24, sept jours sur sept, 365 jours par an. Elle intervient directement sur place pour remédier aux pannes éventuelles et rétablir la disponibilité de livraison dans les plus brefs délais. Les problèmes mineurs, qui ne peuvent jamais être complètement exclus, peuvent être résolus par l'équipe de maintenance professionnelle Omega ou par le système d'assistance-dépannage mis en place par Stöcklin via l'accès à distance.
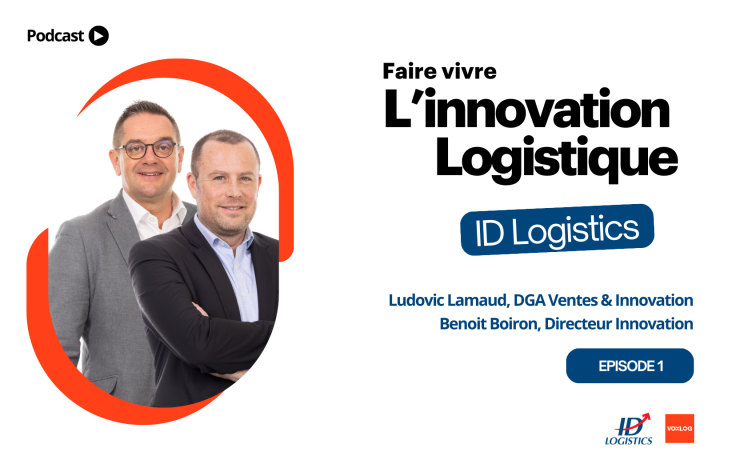