International
Still automatise l'intralogistique de l'usine Nestlé de Biessenhofen, en Allemagne
Still déploie des gerbeurs automatisés EXV iGo et son système Still Pallet Shuttle sur le site de production de Nestlé, dans la ville bavaroise de Biessenhofen. Six entrepôts dédiés aux emballages des produits ont été réunis dans un bâtiment unique.
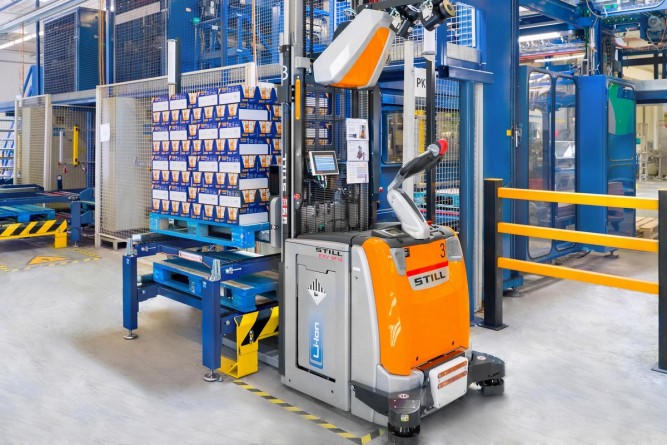
©
Still
Still réalise l'automatisation des flux intralogistiques d'une usine de l'entreprise agroalimentaire Nestlé implantée à Biessenhofen, en Allemagne. Sans stopper l'activité du site, le fournisseur d'appareils de manutention a réorganisé ce lieu caractérisé par des allées des étroites, générant des goulets d'étranglement et des encombrements réguliers en entrée et sortie des machines de production. Après avoir effectué un inventaire et modélisé numériquement les bâtiments, les équipements et les processus, Still a installé, dans les délais et ayant recours temporairement à des chariots élévateurs manuels, quatre gerbeurs automatisés EXV iGo et un Pallet Shuttle. Ce nouveau matériel a permis à Nestlé d'accroître les flux, de gagner en flexibilité et de mieux sécuriser les processus.
Des gerbeurs EXV iGo
L'EXV iGo est un gerbeur automatisé se déplaçant à une vitesse maximale de 1,7 m/s, et pouvant stocker jusqu'à une hauteur de 3 m. Si nécessaire, il est possible de le faire basculer en mode manuel simplement. Au sein de l'entrepôt, il est utilisé pour transporter les matières premières et les emballages jusqu'aux lignes de production 24h/24 et 7j/7 en flux continu, et prendre en charge l'enlèvement des matières recyclables et le restockage des palettes vides. Le mode de production a pu ainsi passer de la méthode « flux poussé » à la méthode « flux tiré », en flux plus tendus. Dotés d'un scanner laser à 360°, les AGV circulent en toute sécurité dans les allées. « Le système automatisé de Still se gère tout seul, explique Bruno Chambraud, responsable du département Intralogistique chez Still France. Il n'y a pas d'interface informatique entre la boucle de commande Still et le système hôte Nestlé. Autrement dit, nous n'avons pas à nous soucier d'un système de transport qui viendrait s'ajouter à la structure informatique déjà complexe de Nestlé. Le transport s'organise tout seul ».
La technologie Still Pallet Shuttle
Ces différentes évolutions ont débouché sur la suppression de six entrepôts stockant des emballages et des accessoires de production, et de leur regroupement en un seul avec un système de rayonnage par accumulation desservi par le système Still Pallet Shuttle. Grâce au stockage et à la récupération semi-automatisés, chaque couloir d'accumulation gère indépendamment son remplissage de marchandises. Par rapport aux rayonnages simple accès (drive-in) desservis manuellement par entrée du chariot dans chaque couloir, la technologie Still Pallet Shuttle renforce la sécurité, améliore le rendement et libère de l'espace.
À lire également : Jacques Arrighi nommé directeur général de Still France
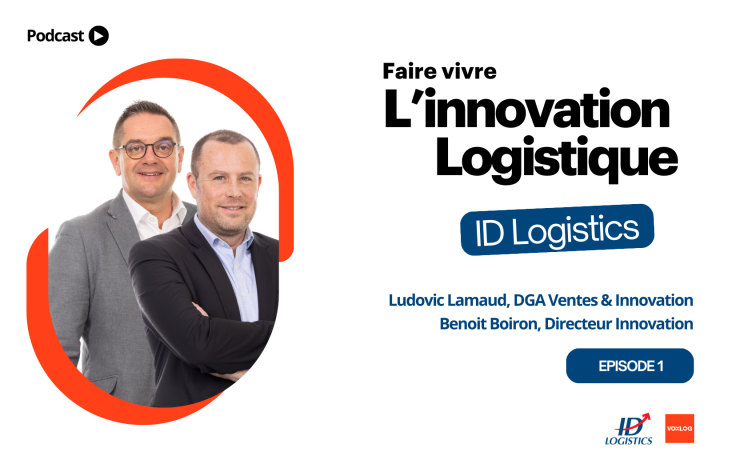