Entrepôts
Transitic installe un système intralogistique respectant la chaîne du froid dans l'entrepôt Maximo de Cerisé (61)
L'entreprise alimentaire Maximo a fait appel à Transitic pour optimiser les flux logistiques et gagner en productivité, au sein de sa récente plateforme basse température implantée à Cerisé, en Normandie. Convoyeurs, machines automatiques et robots fonctionnent en synergie, en conformité avec les strictes exigences du secteur agroalimentaire liées à la continuité de la chaîne du froid.
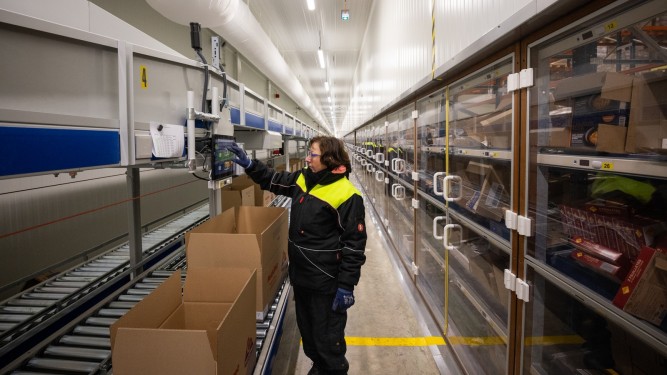
©
ACH photo
Maximo, spécialiste de la livraison de surgelés à domicile, a équipé son entrepôt de 17 000 m² inauguré en 2023 à Cerisé, dans l'Orne, d'un système intralogistique monté par Transitic. Les installations conçues permettent d'améliorer la productivité, de diminuer la pénibilité de travail et de limiter le nombre d’erreurs dans la préparation des commandes. Elles respectent scrupuleusement les normes de sécurité et d’hygiène, et la continuité de la chaîne du froid. Les matériaux choisis, qu’ils soient mécaniques ou électroniques, fonctionnement durablement dans les zones à -25 °C. Transitic a déployé un réseau de convoyeurs de 1,2 km de long qui parcourt l’intégralité de l’entrepôt pour alimenter tout le processus de préparation.
Des prestations mécaniques, robotiques et informatiques
« Pour ce projet, nous avons fait appel à l’ensemble de nos savoir-faire avec des prestations mécaniques, électroniques, informatiques ou encore robotiques », précise Jérôme Paque, directeur Projets chez Transitic. Deux formeuses de cartons multiformats ont été placées en zone de lancement. Une étiqueteuse et un scanner de contrôle s’assurent de la traçabilité de chaque carton. 1 150 systèmes Pick-to-Light, composés de voyants lumineux et écrans digitaux, ont été installés afin de guider les opérateurs dans le prélèvement des produits. Ils sont complétés par des écrans de contrôle et des scanners qui assurent un suivi permanent des commandes.
Avec plus de 16 000 cartons fournisseurs consommés chaque jour, il a fallu prévoir un convoyeur aérien à bandes le long de la ligne de préparation pour permettre aux opérateurs d’évacuer rapidement les contenants vides vers des compacteurs. Une fois le prélèvement des produits terminé, chaque carton circule sur une balance dynamique avant d’être envoyé vers trois postes ergonomiques de contrôle assistés.
Dans une zone à -25°C, un buffer-séquenceur a été implanté. Composé de 10 lignes de convoyeurs, il permet de trier les commandes selon leur tournée de livraison et de stocker les cartons en attente de transfert. Une fois sortis du buffer, les cartons sont chargés automatiquement dans des roll-conteneurs grâce à cinq robots palettiseurs. Ces derniers fonctionnent dans un environnement réfrigéré à 5°C, et respectent l’ordre de livraison des cartons avant leur chargement dans les camions.
L’ensemble du système (convoyeurs, machines et robots) est piloté par les logiciels Open WCS et Open SCP de Transitic.
À lire également : Transitic propose l'intégration du système robotique Infinity d'Opex
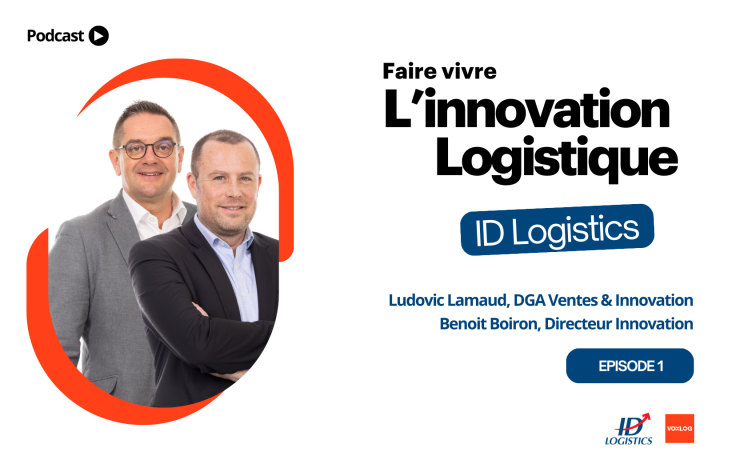