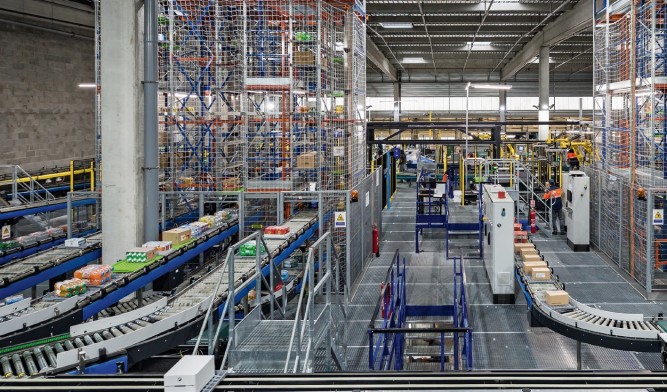
©
U Log
Entrepôts
Chez U Logistique, une automatisation menée depuis plus de cinq ans
En collaboration avec son partenaire Fives, U Log, entité logistique de la Coopérative U, mène depuis plus de cinq une succession de projets afin d’installer des solutions mécanisées et automatisées dans ses entrepôts, aussi bien pour les produits secs que frais. Ronan Le Corre, directeur général de Ulogistique, revient sur une mutation logistique qui se poursuit.
Comment s’organise U Log en France ?
Nous disposons de 27 entrepôts et 6 000 collaborateurs en France pour une surface totale de 1,5 million de m². Nous avons trois grands types d’entrepôts : treize consacrés aux produits frais, dont quatre pour le surgelé ; onze dédiés à l’ambiant alimentaire (épicerie, liquides, hygiène) ; et enfin trois de type bazar : textile, saisonnier, etc. 1 800 de nos camions roulent chaque jour pour livrer 1 600 points de vente, de différents formats, notre coeur de métier restant le supermarché.
D’où est venu votre besoin d’automatisation ?
Nous avons débuté sur le sujet il y a un peu plus de 20 ans, avec des projets de mécanisation pour l’amélioration des conditions de travail, avec une première installation de triage de produits surgelés pour permettre à nos salariés de passer moins de temps en chambre froide. Nous avions également travaillé à l’automatisation de la préparation des fruits et légumes, et des activités de textile avec du goods-to-person. Mais il y a huit ans, nous avons décidé d’aller plus loin. C’est à ce moment-là que j’ai rencontré l’entreprise Syleps (devenue Fives depuis), avec laquelle j’ai collaboré pour automatiser 30 % des volumes de nos entrepôts ambiants, pour des produits lourds et liquides. En effet, notre activité est très saisonnière, avec une présence renforcée de nos magasins sur les côtes Atlantique et Méditerranéenne. L’été, dans nos entrepôts ambiants, 40 à 50 % des volumes sont liés aux liquides, des colis lourds pour lesquels nous avons souhaité aller vers des solutions plus complètes. Il s’agissait de projets importants, avec des investissements de 10 à 12 millions d’euros par entrepôt, visant des ROI ne dépassant pas une dizaine d’années, afin de garder une certaine réactivité.
Comme se déploient ces solutions dans vos entrepôts ?
C’est un projet de mécanisation totale : les opérateurs ne touchent plus les colis. Les palettes homogènes arrivent, sont dépalettisées automatiquement, stockées, puis le système se charge de produire des palettes hétérogènes pour nos magasins. Nous avons ensuite une mise à quai avec des AGV. Il n’y a plus aucune manipulation humaine après la réception. Dès la première installation, il y a cinq ans près de Saint-Brieuc, nous avons été convaincus et avons souhaité poursuivre la collaboration avec Fives. Aujourd’hui, six systèmes de ce type ont été installés sur nos onze entrepôts de produits ambiants, traitant entre 30 000 et 35 000 colis par jour (sur 120 000 colis au global). La gamme intégrée à la mécanisation peut varier selon les périodes et la demande, avec un focus sur les boissons en été par exemple. Depuis deux ans, nous avançons également sur la question du frais. Les problématiques y sont différentes : plus d’hétérogénéité et de flux tendus. Malgré des process digitalisés avec des radios vocales pour assister les opérateurs, le risque d’erreur est plus important pour ce type de produits. Nous avons besoin de fiabilité plus que d’une augmentation de la productivité. Le choix a donc été fait de retravailler avec Fives pour l’installation de dix trieurs, en cours de déploiement. Le premier fonctionne depuis novembre 2019. Ces trieurs traiteront les produits en flux tendus, c’està- dire 65 % des volumes d’un entrepôt frais (sur 150 000 colis quotidiens), les systèmes mécanisés pour les fruits et légumes continuant de couvrir eux 25 % des flux, et le picking vocal se poursuivant pour les 10 % des produits restants, principalement venus de petits fournisseurs. D’ici 2022, tous nos entrepôts frais seront équipés de ce type de trieurs. L’investissement représente sept millions d’euros environ par machine.
Quelles sont les contraintes quant à leur installation ?
Nous souhaitons qu’elles puissent rentrer dans des entrepôts standard, car nous ne construisons pas de bâtiments spécifiques. Pour le sec, il s’agit d’optimiser au maximum la hauteur. L’installation prend en général six mois, et occupe des cellules de 6 000 m², avec des rayonnages allant jusqu’à 10 mètres de haut. Les contraintes sont moins fortes pour les trieurs dans les produits frais, mais il reste nécessaire de libérer 6 000 m² pour des travaux d’une durée moyenne de quatre mois. Dans tous les cas, pour conserver un retour sur investissement maitrisé, il faut qu’un site sorte en moyenne 25 millions de colis à l’année.
Comment se déroule la conduite du changement pour les équipes ?
Tout d’abord en partageant notre plan stratégique chaque année avec nos collaborateurs et partenaires sociaux, les invitant à aller voir les installations et en échangeant avec eux sur le sujet. De plus, nous sommes en croissance constante depuis des années : nous pouvons donc mettre en place ces mécanisations sans remettre en cause l’emploi. Les personnes qui gèrent ces installations sont nos collaborateurs. Nous ne recrutons pas d’ingénieurs. Nos conducteurs de lignes sont tous d’anciens préparateurs ou caristes, ce qui propose donc une évolution intéressante à nos salariés.
Quels sont vos projets à plus long terme sur le sujet ?
Nous nous interrogeons au niveau du stockage. Nos entrepôts sont de plus en plus grands : pour les produits frais, nous avons des sites allant jusqu’à 30 000 m², et dépassant 70 000 m² pour le sec. Afin d’éviter l’inflation de nos mètres carrés, nous commençons donc à réfléchir à la verticalisation de nos entrepôts, avec potentiellement des bâtiments grande hauteur, atteignant 20 à 25 mètres, et nécessitant donc des installations automatisées. Un de nos entrepôts pourrait être éligible dès l’année prochaine pour ce type de projet.
> À lire également, une interview de Thierry Le Chêne, directeur général adjoint de Fives Syleps : Comment Fives apporte son expertise de l’automatisme à l’intralogistique
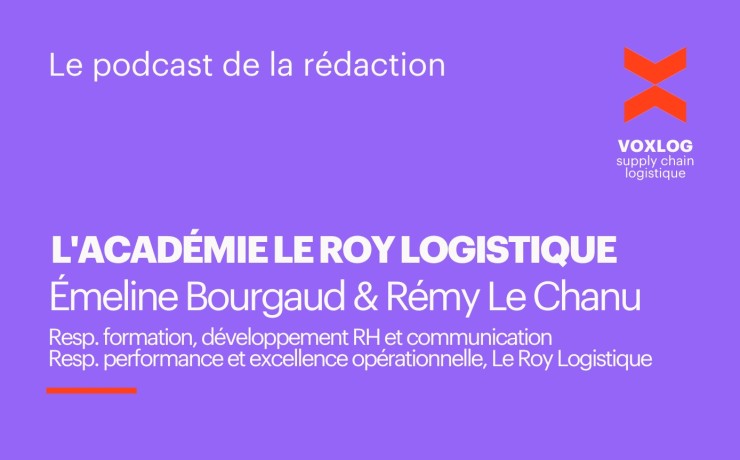