Entrepôts
À l’automatisation des entrepôts vient désormais répondre celle des fournisseurs de palettes. Face à ce mouvement qui devrait se poursuivre à l’avenir, les critères d’exigences du support de manutention s’accentuent.
Dynamique amorcée bien avant la crise sanitaire, l’automatisation chez les industriels et les distributeurs enregistre une accélération ces trois dernières années, avec des investissements en intralogistique visibles chez les principaux acteurs de la grande distribution et chez les industriels. Pour Didier Maréchal, chez Smart-Flow, dans ce contexte de mécanisation croissante, les palettes en plastique représentent « un avantage majeur » pour les sites logistiques automatisés : « Ils ont la garantie de disposer de produits tous identiques avec une tare constante, ce qui n’est pas le cas des palettes bois dont le poids varie en cas d’humidité et de pluie », juge-t-il.
Des exigences accrues
Au développement de cette mécanisation correspond une évolution du cahier des charges pour l’utilisation des supports de manutention bois : « Les contraintes d’aujourd’hui n’ont à rien à voir avec celles d’il y a cinq-six ans, en matière d’automatisation et de productivité des outils utilisés par nos clients, détaille Hervé Fourcade, directeur commercial de LPR France. Si la palette traditionnelle pour l’agroalimentaire est normée et que ses dimensions demeurent de 80 x 120 cm, les tolérances qui existaient par le passé côté fabrication ou utilisation sont aujourd’hui beaucoup plus restreintes ». LPR a ainsi dû s’adapter à cette mécanisation, ses palettes locatives étant amenées à être manutentionnées de nombreuses fois, entraînant une usure des planches, des plots et des semelles. Or, les exigences en « manque de matière » bois (portant sur le taux d’usure de la palette) s’étant durcies, elles ont imposé à l’entreprise une augmentation du taux de réparation de ses palettes après contrôles et tri pour répondre aux contraintes des outils de stockage et de manutention : « Cela nous oblige à des investissements assez importants sur nos centres de service pour automatiser tout ce qui est tri et réparation, avec des calibreuses qui vont respecter des dimensions, et surtout des manques de matière que nous n’avions pas auparavant », poursuit Hervé Fourcade.
Cette mécanisation croissante des sites a également impacté les process du groupe PGS qui vient pallier les aléas naturels du bois par davantage de surveillance et de vérifications : « Nous avons mis en place énormément de robotisation, de contrôle de planéité, de détecteur de clous dépassants, pour pouvoir dire à nos clients qui utilisent ces entrepôts ultra-automatisés, qu’ils peuvent travailler sereinement avec une palette bois. Nous avons même développé des systèmes automatisés pour nettoyer les palettes en bois afin de les rendre aptes aux contraintes sanitaires de nos clients », détaille Michael Modugno, vice-président fondateur du groupe.
Répondre aux différents besoins
À l’automatisation des entrepôts va donc correspondre celle des fournisseurs de palette, ces derniers étant désormais amenés à entrer en communication de plus en plus rapprochée avec les acteurs de l’intralogistique : « Lorsque ceux-ci étudient un entrepôt pour un industriel ou un distributeur, nous réalisons des tests ensemble et nous envoyons les plans des supports. Il faut que les tolérances de leur outil correspondent aux nôtres. Alors qu’il y a quelques années, nous étions simplement des fournisseurs de palettes, aujourd’hui nous avons une équipe d’ingénieurs méthode en relation avec nos clients qui interviennent en amont des projets pour apporter notre savoir-faire et les accompagner sur des tests », poursuit Hervé Fourcade. Même constat chez IPP : « Sans toucher à la palette elle-même, qui demeure un standard de la distribution partout en Europe, les entrepôts automatisés de certains distributeurs imposent des critères qualité forts pour éviter des taux de rejet trop importants sur leur ligne mécanisée », confirme Laurent Martin, directeur commercial d’IPP France.
Et la palette Europe gérée par un prestataire de services s’adapte aussi à ces nouvelles contraintes, proposant, parmi cinq niveaux de qualité – neuve, comme neuve, mécanisable, triée, échangeable transporteur –, un usage spécial dédié aux centres automatisés via la « palette mécanisable » : « Elle passe par un tri supplémentaire chez des recycleurs normés Epal pour vérifier l’alignement des plots et le respect de la périmétrie. Venue d’Allemagne il y a 10 ans où elle a obtenu le label environnemental Blue Angel, elle se standardise de plus en plus sur le marché français », détaille Fabrice Chenut, directeur des ventes France/Ibéria de Paki. La société est ainsi en mesure de livrer chacune des cinq qualités exigées par un site industriel ou une base de la grande distribution : « Nous répondons aux besoins de tout type de société. Certaines vont se satisfaire, pour du picking par exemple, d’une palette échangeable classique, avec une qualité triée, tandis que d’autres, comme celles de la grande distribution, vont requérir de la palette mécanisable ». Une manière également de montrer que la palette normée Europe peut s’adapter aux nouvelles exigences du métier et à sa mécanisation croissante.
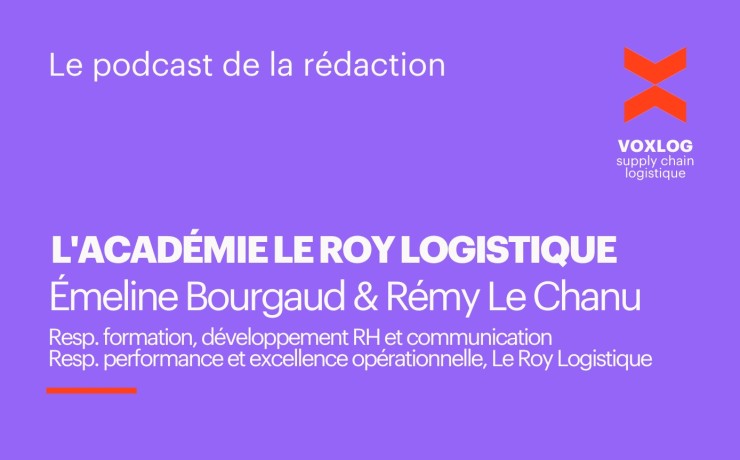