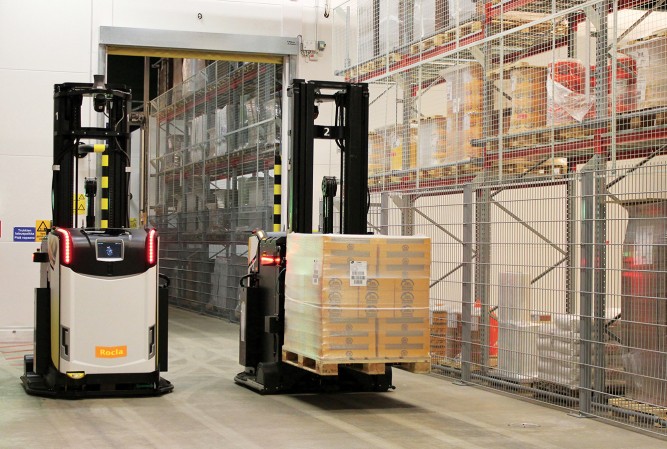
©
Aprolis
Entrepôts
AGV et AMR : l'automatisation mobile s'invite en entrepôt
S’ils restent un marché de niche dans le monde des équipements de l’intralogistique et de l’industrie, les AGV et AMR continuent de se faire une place au sein des entrepôts et des sites industriels modernes, offrant une vision de l’automatisation flexible, efficace et innovante. Des constructeurs et experts dévoilent leur vision du marché et les perspectives apportées par ces véhicules
Ils parcourent les allées des entrepôts, avançant souvent seuls, mais parfois accompagnés, suivant des repères au sol ou se dirigeant grâce à une cartographie prédéterminée du site qu’ils arpentent. Dotés de nombreux capteurs pour éviter tous risques d’accidents ou de collisions, ils sont capables de déplacer de multiples charges et de répondre à des besoins toujours plus variés : qu’on les appelle AGV (Automated guided vehicle, ou véhicule à guidage automatique) ou AMR (Autonomous mobile robot ou robots autonomes mobiles), les équipements d’automatisation mobile sont maintenant une figure familière en entrepôt. Et si l’AGV se déploie sur des sites logistiques et industriels depuis plusieurs décennies, il a récemment été rejoint par son cousin l’AMR pour automatiser différents process.
Un marché de niche qui attire l'attention des entreprises
En France, comme ailleurs dans le monde, leur utilisation reste principalement réservée à un nombre limité d’entreprises, représentant un marché de niche. « Les ventes d’AGV tournent entre 500 à 600 machines à l’année dans l’Hexagone, avec quelques acteurs constructeurs ayant pu prendre des parts de marché intéressantes de par leur présence depuis plusieurs années. La moyenne de vente par projet ne bouge pas, restant à trois ou quatre machines. Il y a quelques flottes plus larges, mais cela reste ponctuel », détaille Yannick Antoine, directeur opérationnel des solutions logistiques chez Toyota Material Handling France. « La part des AGV reste minime pour l’instant en comparaison du marché du chariot manuel même si la croissance est importante chaque année, confirme Bruno Chambraud, responsable du département intralogistique chez Still France. De plus, là où le marché du chariot manuel est basé sur le renouvellement, avec des changements de flottes plus fréquents, les AGV sont eux amenés à durer plus longtemps, réduisant le nombre d’unités vendues ».
Cependant même si le sujet de l’automatisation mobile reste relativement confidentiel en termes de volumes face à un marché global de l’intralogistique dynamique, son développement se poursuit et l’intérêt des acteurs de l’industrie et de la supply chain ne se tarit pas, bien au contraire. « Les entreprises du secteur voient que la technologie avance, que les projets se multiplient et elles s’y intéressent d’autant plus. Nous avons des demandes régulières pour voir simplement ce que cela pourrait donner en termes de coûts, même si l’automatisation reste encore une enveloppe complexe à budgéter pour certains clients », constate Bruno Chambraud. Un avis que partagent de jeunes entreprises robotiques en pleine croissance comme Mobile Industrial Robots (Mir) : « L’automatisation des flux va se poursuivre et s’accélérer dans les cinq à dix prochaines années. Si on voyait jusqu’ici principalement de petits déploiements, avec un robot ici où là, de plus en plus de projets prévoient des flottes de robots plus grandes, pouvant réunir 30 ou 40 unités sur la même usine. Même ceux qui ont peur de se lancer sur le sujet pour des raisons de capacité financière vont finir par le faire, y compris les plus petites entreprises », déclare Olivier Pommares, responsable commercial France chez Mir.
Des technologies différentes mais des usages communs
Mais quelles sont les différences entre les deux types de solutions ? Elles tiennent en plusieurs paramètres. Les AGV sont des véhicules qui se déplacent de manière autonome en suivant un chemin prédéterminé, selon des marquages au sol ou des éléments électromagnétiques qui ont été installés dans l’entrepôt. Ils travaillent donc sur des circuits fermés et définis. De par leur navigation guidée, quand un obstacle est sur leur chemin, ils s‘arrêtent, et reprennent leur route quand celuici est parti. Si l’on veut changer la trajectoire de ces AGV, il faut donc faire évoluer l’infrastructure et son marquage dans l’entrepôt. Les ARM, eux, fonctionnent sur une technologie de navigation différente : avant leur installation dans l’entrepôt, une cartographie précise du site est réalisée, définissant une multitude de positions depuis lesquelles des actions seront effectuées. Quand celle-ci est complétée, l’ARM va pouvoir recevoir différentes missions, impliquant d’aller d’un point A à un point B. C’est lui qui décidera ensuite, selon des règles établies et l’intelligence de son système de navigation, quel trajet prendre pour effectuer ce mouvement, capable donc d’éviter ce qui se présenterait sur son chemin (opérateurs ou objets) grâce à ses systèmes de sécurité. Mais certains notent que l’opposition entre les deux équipements peut être un simple argument marketing alors que leurs technologies et usages sont proches.
« L’ARM se déplace sur des surfaces plutôt que des lignes comme un AGV, mais la frontière entre les deux mondes est fine car nous sommes capables de mettre en place tout un réseau de routes avec les AGV qui peuvent apporter les mêmes avantages : sur des AGV de marque Rocla que nous proposons, si une zone est bloquée par un engin, les autres AGV peuvent en être informés et la contourner, proposant donc un usage proche de l’AMR », note Jérémy Cimelli, ingénieur robotique du département AGV chez Aprolis, loueur de solutions pour la manutention. Un regard que partage Sébastien Dumon, chef de produit solutions intralogistiques chez Alstef Group : « On sépare souvent AGV et AMR alors qu’ils sont complémentaires. Si on vise de la cadence et des flux fixes, les technologies d’évitement d’obstacles de l’AMR ne vont pas être pertinentes, car on préfèrera automatiser sur des routes bien définies avec un système AGV et conseiller le client pour que ce chemin soit toujours libre, plutôt que de programmer des technologies d’évitement et d’adaptation de trajectoire qui pourraient faire perdre du temps. Certaines organisations ont cependant besoin d’AMR pour desservir des ateliers en mode collaboratif, pour apporter des pièces en production, qui ne pourraient pas être accessibles à un AGV. Il existe également une différence en termes de capacité : les AGV sont capables de porter une tonne là où les AMR traitent souvent des charges plus légères ».
Des AGV et AMR, pour quoi faire ?
Pour les constructeurs, l’automatisation mobile en entrepôt est avant tout un levier de performance supply chain et une technologie capable de décharger les équipes des tâches les plus répétitives et pénibles de leurs métiers. « L’utilisation de chariots automatisés est pleinement justifiée notamment pour certaines applications comme des missions de transfert d’un point A à un point B. Cela permet de redéployer les opérateurs vers des missions à plus forte valeur ajoutée », résume Christian Sauzin, directeur ventes et marketing chez Fenwick-Linde. « L’automatisation est dédiée à la répétitivité. Il faut des charges et des supports homogènes, qui vont être traités avec des mouvements simples » note Yannick Antoine chez Toyota Material Handling France. Les AGV peuvent ainsi se déployer d’un bout à l’autre de la chaîne d’approvisionnement, allant de la prise en charge des palettes sur les quais à leur mise à disposition sur les lignes de production, dans les zones de stockage, ou pour la préparation de commandes. Comme toujours pour ce type de projets, les constructeurs soulignent que le but de la robotique n’est pas de venir remplacer l’humain dans les sites logistiques : « C’est une collaboration avec les systèmes manuels, et pour les caristes, ces changements sont souvent bien acceptés, car ils ne veulent pas spécialement faire du roulage sur des kilomètres dans l’entrepôt », déclare Yannick Antoine.
Il convient également de ne pas faire d’équivalences entre les missions d’un humain et celles d’un robot. Au contraire, les process de l’AGV vont parfois être très différents par rapport à l’existant, en divisant par exemple une action manuelle complexe en plusieurs mouvements simples pour les AGV : « Il faut casser l’idée, encore trop fréquente, que l’installation d’un AGV consiste simplement à remplacer un cariste par un robot. Quand on mène un projet de ce type, il faut définir une solution adaptée aux besoins du client sans tenir compte de la façon dont il traite le sujet aujourd’hui », note Jérémy Cimelli chez Aprolis. Enfin, pour des raisons techniques ou d’efficacité, tout flux réalisé par des humains n’est pas forcément automatisable. « Il y a quelques années, on observait certains effets de mode sur le sujet, avec une recherche du moindre flux automatisable même quand ce n’était pas pertinent. Cette tendance a baissé et les gens savent maintenant ce qu’ils veulent automatiser », note Yannick Antoine. Un constat fait par plusieurs constructeurs du secteur, qui soulignent la maturité grandissante des entreprises sur le sujet, particulièrement dans le monde de la logistique. « Pendant longtemps, les industriels essayaient de gagner de la productivité sur leurs lignes de production et la logistique était mise de côté. Ces derniers temps, ce mouvement d’automatisation s’étend enfin vers la logistique, qui est devenu un enjeu majeur, notamment avec l’explosion du e-commerce », note Sébastien Dumon, chez Alstef Group.
Ainsi, chez Sherpa Mobile Robotics, qui avait à l’origine une cible principalement industrielle via sa société mère Norcan, ses solutions AMR s’ouvrent désormais au e-commerce, au retail et à la logistique. C'est le cas chez Fnac, un de ses premiers clients : « Dans leur nouvelle organisation des opérations de picking avec l’aide de nos robots, l’opérateur reste dans des zones définies de l’entrepôt et va se concentrer sur les missions de préparation ou de remplissage de rayons. Notre robot Sherpa B vient à lui, le suit grâce à ses nombreux capteurs et transporte les charges lourdes à sa place, puis repasse en mode autonome pour réaliser la mission qu’on lui indiquera : rejoindre un autre opérateur situé dans une allée voisine, se rendre dans une zone d’évacuation pour déposer les produits sur un convoyeur, ou bien passer par une zone d’emballage. Le champ des possibles est vaste ! », affirme Arnaud Debs, responsable marketing chez Sherpa Mobile Robotics.
De l'automatisation aux multiples usages et bénéfices
Qu’importent leurs formats et déclinaisons, les solutions automatisées et autonomes offrent toutes de nombreux avantages dans l’entrepôt. Des gains de performance importants, en évitant aux employés de perdre du temps avec des opérations de roulage et de simple transfert de charges. Plus de fluidité également, avec des AGV et AMR qui alimentent les zones de préparation ou d’expédition avec un fonctionnement just-in-time, amenant les bons produits, au bon endroit et au bon moment. On note aussi plus de sécurité en entrepôt, grâce aux nombreux systèmes embarqués sur les robots (lasers, capteurs, cameras 3D pour la navigation…). Des équipements qui suivent la nouvelle norme ISO 3691-4, entrée en action l’année dernière et ayant élevé le niveau d’exigence pour ces chariots automatisés. « On ne tolère pas d’accidents sur des équipements de ce type. La robotique est contrainte à la sécurité à 100 %, ce qui n’est pas le cas d’un opérateur humain. Si les normes à respecter sont très contraignantes elles permettent d’assurer que le robot ne fera pas d’erreurs », remarque Jérémy Cimelli. La flexibilité est également un mot clé pour de nombreux acteurs : face à une forte complexité des flux dans un contexte où les demandes de consommateurs nécessitent des logistiques plus réactives, les organisations supply chain ont besoin de pouvoir évoluer et de s’adapter sans complètement remettre en question leur organisation interne.
« L’automatisation traditionnelle se base sur des infrastructures fixes qui, si elles sont très efficaces, sont parfois couteuses et difficiles à ajuster. Avec des systèmes robotiques adaptables, basés sur l’IA, les entreprises ont la flexibilité recherchée pour traiter non seulement l’incertitude des pics d’activités, mais aussi les doutes associés à la croissance d’un business sur le long terme », note Jackson Zhang, viceprésident de l’entreprise robotique Geek+ Europe. Pour cela, les constructeurs insistent sur la capacité laissée aux utilisateurs fi naux de reprogrammer leurs systèmes automatisés. « Pas besoin d’avoir des roboticiens en interne, un opérateur ou un chef de projet peut prendre en main la machine via nos interfaces intuitives. Au moment de l’intégration, nous dispensons une formation qui permet au client final d’être autonome dans l’utilisation de ses robots », assure Arnaud Debs chez Sherpa Mobile Robotics. « Il est crucial que s’effectue un transfert de compétences, et que le client puisse changer sa solution selon ses besoins. Nous avons développé des interfaces très simples, utilisables sans l’intervention d’un intégrateur », assure de son côté Olivier Pommares, de Mir. De manière générale, les constructeurs remarquent que les lignes bougent du côté de la logistique, avec des entreprises qui font le pari de l’automatisation. « Les AGV ne sont pas liés à un site et il est possible de les déplacer. Un de nos clients procède ainsi pour pallier aux activités parfois variables de ses différents entrepôts. Les acteurs de la profession sont désormais convaincus des bénéfices qu’ils peuvent tirer des solutions automatisées sur leur exploitation. La phase de découverte dépassée, ils veulent des simulations concrètes, avec des rendements de palettes à l’heure », juge Christian Sauzin chez Fenwick-Linde. Et certains notent aussi l’effet vitrine que peut représenter ce type de véhicules pour des acteurs logistiques souhaitant se démarquer. « Ces nouvelles technologies sont des éléments différenciants pour nos clients. Nous observons cette tendance chez certains prestataires logistiques par exemple », remarque Éric Deffontaines chez Jungheinrich
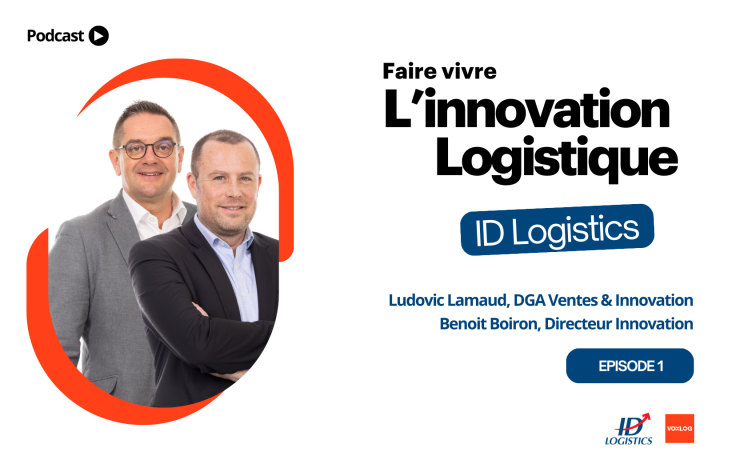