Entrepôts
3. Exemple de transformation : Pileje rentabilise son automatisation
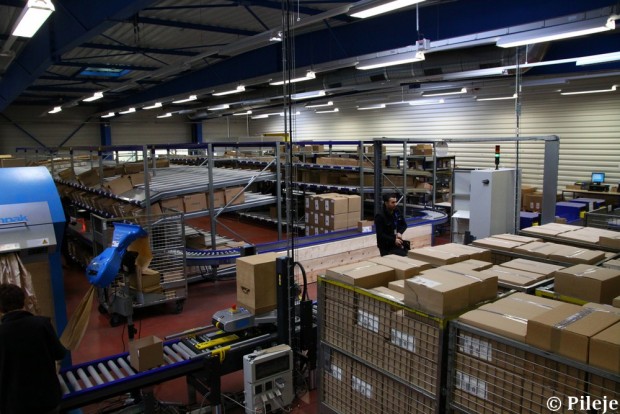
Créé il y a 25 ans par le docteur Christian Leclerc, le laboratoire Pileje distribue des compléments alimentaires et des produits de phytothérapie à travers un réseau de pharmacies. Pour répondre à sa forte croissance, le groupe a fait le choix d’automatiser son entrepôt de Saint-Laurent des Autels, dans le Maine-et-Loire (49). Une nouvelle organisation qui lui a permis de devenir le numéro 2 français du marché du complément alimentaire en pharmacie.
En 2011, les commandes clients du laboratoire Pileje étaient préparées presque intégralement à la main. Le pilotage de l’entrepôt était uniquement manuel. Pour accroître sa capacité de production, le groupe décide en 2012 de modifier son organisation logistique en automatisant son entrepôt. Deux options se sont ainsi imposées : conserver l’automatisation logistique et la préparation de commandes en interne ou l’externaliser.
Pileje, afin de conserver le même nombre d’employés, opte pour l’internalisation. « Nous avons réfléchi à plusieurs solutions tout en benchmarkant l’externe », explique Jean- Pierre Couedic, directeur supply chain de Pileje. « Nous nous sommes aperçus qu’une solution interne semi-automatisée ne nous coûterait pas plus cher, permettrait de garder notre effectif, ce qui était quand même un souhait premier de notre direction, d’apporter une réactivité pour passer les pics de production et surtout de garder une souplesse d’adaptation aux besoins marketing », développe-t-il. Suite à un appel d’offres, quatre entreprises viennent effectuer une démo de leur outil. Pileje choisit Fives pour mettre en place un convoyeur automatisé destiné à la préparation de détail. Y est adjoint le logiciel de gestion d’entrepôt Acteos WMS (ex. Logidrive) d’Acteos.
Un changement d’organisation parfois difficile
Satisfait de la collaboration entre Acteos, Fives et son groupe, Jean-Pierre Couedic regrette néanmoins de ne pas avoir pu bénéficier d’assez de délai entre la mise en place des installations et leur lancement. Un manque de temps d’adaptation qu’il explique par la faible expérience du groupe pour ce genre de déploiement. « Entre la phase de démarrage où nous avons conclu le contrat et la phase de production, il s’est écoulé six à sept mois ; il nous aurait fallu trois voire six mois de plus », explique-t-il. Un changement rapide d’organisation du travail qui n’a pas immédiatement plû à tous les employés. Avant la mise en place du convoyeur et du WMS d’Acteos, les opérateurs travaillaient essentiellement par missions. Depuis la mise en place de l’automatisation, une partie des opérateurs s’est adaptée à la nouvelle organisation, se sentant mieux encadrée, plus à l’aise et productive. « Cette nouvelle organisation nous a permis de nouer avec la croissance et de conserver des emplois, c’était vraiment nos objectifs », affirme le directeur supply chain de Pileje.
Des embauches prévues
Au final, les installations ont offert de nouvelles opportunités de carrière. Des profils se sont dégagés pour effectuer du pilotage et ont été promus animateur ou chef d’équipe. La mise en place de l’automatisation a également permis d’accroître la productivité de l’entrepôt en réduisant le temps et le nombre de déplacements des employés. « Hier, nous avions une préparation de commandes qui était manuelle, c’est-à-dire qu’une opératrice gérait par exemple les commandes de pharmacie de A à Z, explique Jean-Pierre Couedic. Aujourd’hui avec l’automatisation, le colis vient à elle et les produits sont disséminés autour d’elle ».
La mise en place du WMS a également permis d’améliorer la traçabilité des produits distribués en pharmacie, en associant de façon très précise un numéro de lot à une commande client. Pileje respecte ses délais de livraison à 98 %, contre environ 85 % avant l’automatisation. Jean-Pierre Couedic indique que la productivité du site a pratiquement doublé en l’espace de trois ans et que le retour sur investissement a duré 26 mois. Pileje commence à faire des tests pour agrandir la plage horaire de production de son convoyeur, en la passant de 7 à 10 heures voire 12 heures. Le groupe prévoit ainsi des embauches en 2017, « si la croissance est toujours aussi forte », pour soutenir l’élargissement potentiel de ses horaires de production.
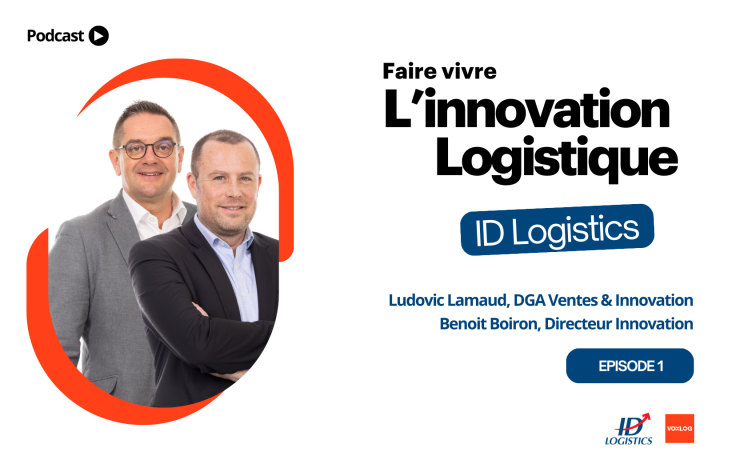