Entrepôts
Automatisation : la logistique industrialisée de la Scapest
Fin 2015, la Scapest, centrale d’achat régionale de E.Leclerc, ouvrait à Recy (51) une plateforme de distribution entièrement automatisée, équipée des technologies de l’intégrateur Witron. Visite guidée de ce site innovant et précurseur aux côtés de son directeur, Olivier Fache.
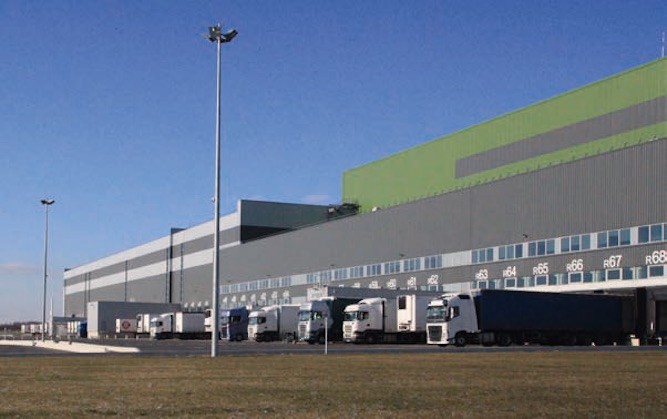
©
Voxlog
Si la mécanisation des flux logistiques s’est démocratisée ces dernières années, rares encore sont les exemples français de sites affichant des solutions automatisées d’un bout à l’autre de la chaîne d’approvisionnement. C’est pourtant le cas depuis plus de deux ans à la Scapest, l’une des 16 centrales d’achat régionales du groupe E.Leclerc. Dédiée à la région Est, elle représente 9 % du chiffre d’affaires du géant de la grande distribution. Une zone stratégique qui a su réinventer sa logistique aux côtés de l’intégrateur bavarois Witron. Le résultat ? Un entrepôt entièrement conçu autour d’une installation automatisée de préparation des commandes magasins au colis. Sur ce site précurseur, la Scapest est capable de traiter jusqu’à 450 000 colis par jour pour un réseau de plus d’une centaine de points de distribution. Le tout dans seulement 43 000 m². « Dans un entrepôt classique, nous aurions besoin de 120 000 m² au minimum ! », affirme Olivier Fache, directeur de la Scapest et instigateur de ce projet innovant (en photo ci-dessus). C’est lui qui a lancé dès 2008, avec des adhérents de la Scapest, une réflexion pour faire face à l’augmentation et la diversification des points de vente, en particulier la montée en puissance des drives. « Personne n’avait anticipé l’arrivée massive de ces nouveaux formats. Leur multiplication soudaine nous a obligé à saturer nos surfaces et dégrader fortement notre productivité. Il fallait agir vite », explique Olivier Fache. Une urgence résumée en quelques chiffres : entre 2005 et 2017, les points de distribution de la Scapest sont passés de 43 à 112. Si le nombre d’hypermarchés est resté stable (entre 41 et 45), celui des drives a explosé pour atteindre 41 en 2017.
Pour y répondre, ce sont vers les solutions d’automatisation de Witron que la Scapest s’est tournée, à l’aune d’une première collaboration réussie entre l’intégrateur allemand et la centrale d’achat voisine Scapalsace, sur leur site de Colmar (68). « Avec ce système, nous sommes en mesure d’assurer la livraison de tous les magasins au meilleur coût. 50 nouveaux points de vente pourraient ouvrir demain, cela ne changerait rien pour nous », résume Olivier Fache. Au total, un investissement de 125 millions d’euros et 27 mois de travaux ont permis l’ouverture du site à l’automne 2015. « Le chantier a nécessité une collaboration très étroite entre les équipes de construction et d’intégration », raconte Olivier Fache. « Le bâtiment devait matcher parfaitement avec le process ». Un travail de fond a également été réalisé auprès des fournisseurs. « La tolérance pour les palettes non conformes, jusqu’ici trop souple, n’est plus possible avec des systèmes automatisés, détaille Olivier Fache. Notre niveau d’exigence n’a pas augmenté. Nous ne demandons que le respect de normes qui existaient déjà auparavant ». Dernier enjeu, la gestion de plus de 15 000 références. Pour être intégrées, une phase de paramétrage a dû être réalisée, afin que la taille, le poids ou la fragilité de chaque produit puisse être pris en compte par l’installation. Un travail réalisé dans les neuf mois qui ont suivi l’ouverture du site. « Chaque semaine, nous basculions entre 200 et 500 références depuis notre précédente plateforme », se souvient Olivier Fache. Aujourd’hui, seuls 3 % des produits ne sont pas pris en charge par la solution (produits hors gabarits, trop souples voire à très faible rotation).
Au coeur de la machine
« Nous ne sommes plus tout à fait dans un entrepôt logistique ». Ces mots, lancés par Olivier Fache le long des allées du site de la Scapest, résument bien le changement profond de paradigme apporté par l’automatisation. À l’exception des activités de réception et d’expédition, la quasi-intégralité du stockage et de la préparation de commandes est réalisée grâce au système OPM (Order picking machinery) de Witron, de manière autonome, intelligente et industrialisée. En entrée, les palettes passent par des portiques chargés d’analyser leur qualité et conformité. Après ce contrôle, les palettes sont amenées en convoyeur jusqu’à deux cellules consacrées à leur stockage. D’une hauteur de 32 m, elles peuvent accueillir un total de 72 800 palettes. Chacune d’entre elles est composée de cinq allées avec des transstockeurs capables de venir ranger les palettes à une vitesse de 4 m/s. « Il n’y a pas de positions attribuées en amont : le rangement s’adapte en fonction de plusieurs règles », explique Jean-Marc Heilig, responsable commercial France pour Witron. « Les produits ayant une forte rotation sont placés au début des allées par exemple. Mais le système va également répartir plusieurs palettes d’une même référence à des emplacements différents afin d’avoir accès à tout le stock même si une allée est inaccessible pour des raisons techniques. »
À cette première étape succède une phase innovante du système : l’éclatement des palettes en colis individuels. Celle-ci débute par la seule action encore gérée par des humains au sein de la solution : le défilmage. « Nous faisons appel au regard et à l’intelligence humaine pour s’assurer qu’une palette et ses produits sont en bon état », détaille Jean- Marc Heilig. Sur un écran, l’opérateur voit le nombre de couches dont le système a besoin. Il prépare alors la palette pour permettre ce prélèvement précis, qui est effectué ensuite automatiquement par aspiration ou serrage selon la typologie des produits. Ces derniers sont ensuite éclatés individuellement via un jeu de convoyeurs et placés sur un support de charge : une tablette en plastique équipée d’un code-barres qui permet d’associer chaque produit à une référence précise. Un système breveté offrant une traçabilité intégrale du colis tout du long de la chaîne logistique. Prochain arrêt : le stock colis, composé de 44 allées réparties sur deux cellules de deux étages. Dans chacune, des miniloads allant jusqu’à 6 m/s, chargés du déplacement des produits selon les commandes à venir. La préparation des commandes débute ensuite avec un passage via des séquenceurs qui réunissent et organisent les colis dans le bon ordre avant d’être envoyés vers les têtes de palettisation. Véritable clé de voute du système, ces dernières vont ensuite préparer avec précision les palettes pour chacun des magasins en respectant des critères standards (poids, taille), en optimisant les volumes et surtout en respectant le séquençage des rayons de chaque point de livraison. « À partir des données cartographiques des points de vente, la machine calcule automatiquement un plan de palettisation totalement optimisé », explique Jean-Marc Heilig. « Aujourd’hui, 80 % des palettes qui arrivent en magasin sont vidées au bout d’une seule allée. C’est un gain de productivité considérable », ajoute Olivier Fache. 520 colis par heure peuvent être traités par chacun des modules, avec un taux d’erreur quasi nul.
Après quoi les palettes sont filmées, étiquetées et mises dans un stock temporaire avant d’être placées automatiquement devant les quais de chargement correspondants pour expédition. Là encore, l’optimisation permise par l’automatisation se manifeste, puisque l’homogénéité des formats des palettes permet à la Scapest de charger désormais ses camions en double étage, offrant ainsi des gains côté transport. Tout autour de la machine, une cinquantaine de collaborateurs se relaient pour veiller à son bon fonctionnement. Un personnel composé d’anciens préparateurs de commandes, venus des précédents sites de la Scapest, dans une optique de maintien des emplois. « Ils ont complètement changé de métier. Ils supervisent le bon fonctionnement de l’installation et gèrent tous les incidents. Si tout se passe bien, ils n’ont rien à faire et on ne les voit pas. Mais au moindre problème, ils sont très réactifs », résume Olivier Fache. Une autre façon de réinventer les métiers logistiques. Si la Scapest compte encore profiter un moment des bénéfices apportés par cette installation (dont la durée de vie est estimée à plus de 20 ans), elle s’est aussi laissée de la place pour des extensions : des zones ont déjà été préparées sur les côtés du bâtiment, principalement pour augmenter les surfaces de stockage mais également les zones de décharge et charge. À Recy, la Scapest semble maintenant parée à toute éventualité.
La Scapest en chiffres
■ 450 000 colis par jour ;
■ 43 000 m² ;
■ 112 points de distribution ;
■ 15 000 références ;
■ 72 800 palettes en stock.
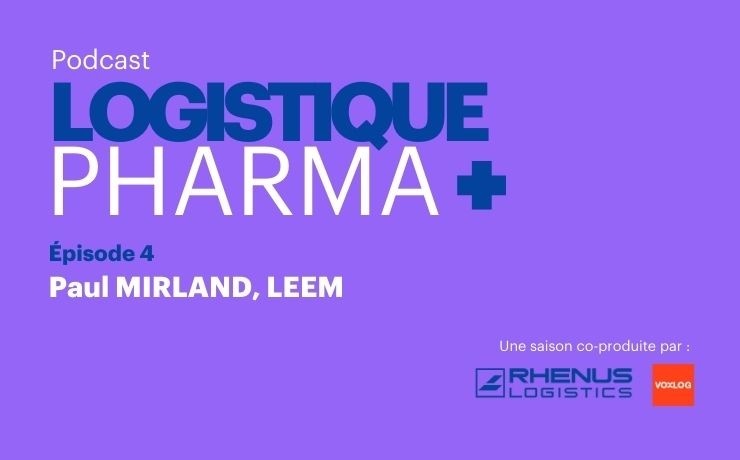